To reduce their carbon footprint, a leading food manufacturer undertook a project to convert from plastic to cardboard packaging trays. In order to achieve this, Asmech provided a wire belt conveyor system. This decision had beneficial environmental and financial savings. However, the new product proved difficult to be transported throughout the existing conveyor system.
Asmech were approached by this customer to design, manufacture and install a solution that could be implemented throughout the factory to improve production and reduce stoppages on the current conveyor system. One of the main issues on the system was that product could not be delivered into the freezers. This meant operators has to hand pack into standalone freezers at an additional cost to the current operation.
Wire Belt Conveyor provided by Asmech
To achieve the task set out, Asmech integrated a slave driven wire belt conveyor to accept product from the existing hinged infeed modular conveyor to transfer trays into the freezer. This system replaced the existing dead plate which was mounted on the infeed to the freezer. To allow the new system to be slave driven to achieve a tight transfer into the freezer, Asmech replaced a drive side plate and shaft on an existing conveyor. This enabled the new wire belt conveyor to be mounted to and driven from. The slave driven arrangement is comprised of a timing pulley. This is mounted to the new and existing conveyor system which is joined by a timing belt.
Enabling Asmech to accept the new trays from the freezer and transfer them onto an existing line. We were required to mechanically remove the existing closed top modular conveyor system from situ and install a new, underslung wire belt conveyor. This conveyor processes quicker than the freezer. Allowing the new tray to be pulled over the transfer area and pushed onto the existing conveyor line.
[Best_Wordpress_Gallery id=”19″ gal_title=”Wire Belt Conveyor Case Study”]
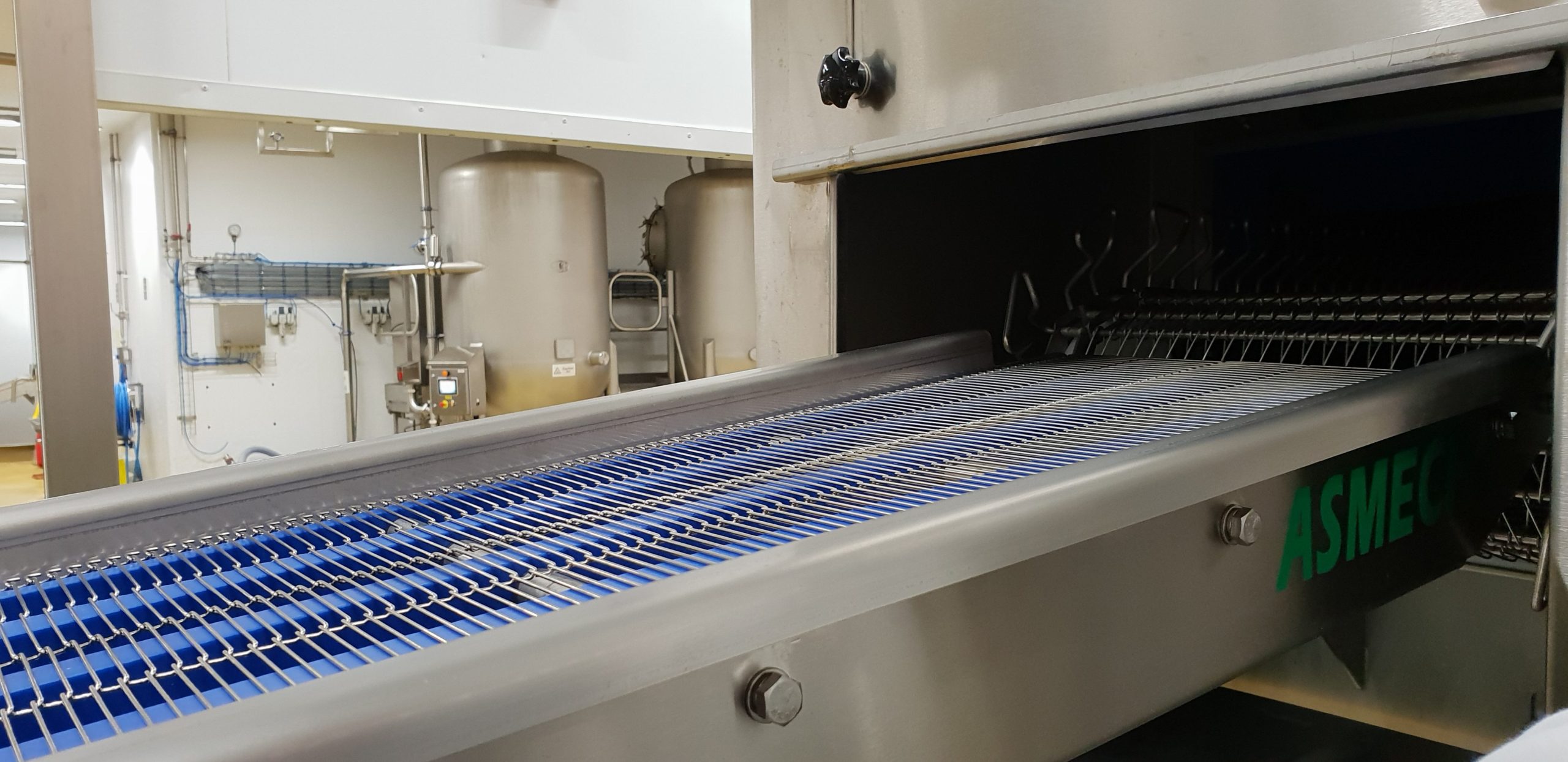